XLPE stands for Cross Linked Polyethylene. This is a type of polymer insulation widely used in electrical power cables, especially in high voltage (HV) and extra-high voltage (EHV) applications. It is derived from polyethylene but has been chemically modified to improve its thermal, mechanical, and electrical properties.
Key Features of XLPE
Cross-Linking Process: In standard polyethylene (PE), the molecular chains are linear. In XLPE, these chains are chemically cross-linked, forming a three-dimensional network. This structure of polyethylene improves heat resistance, mechanical strength, and electrical insulation.
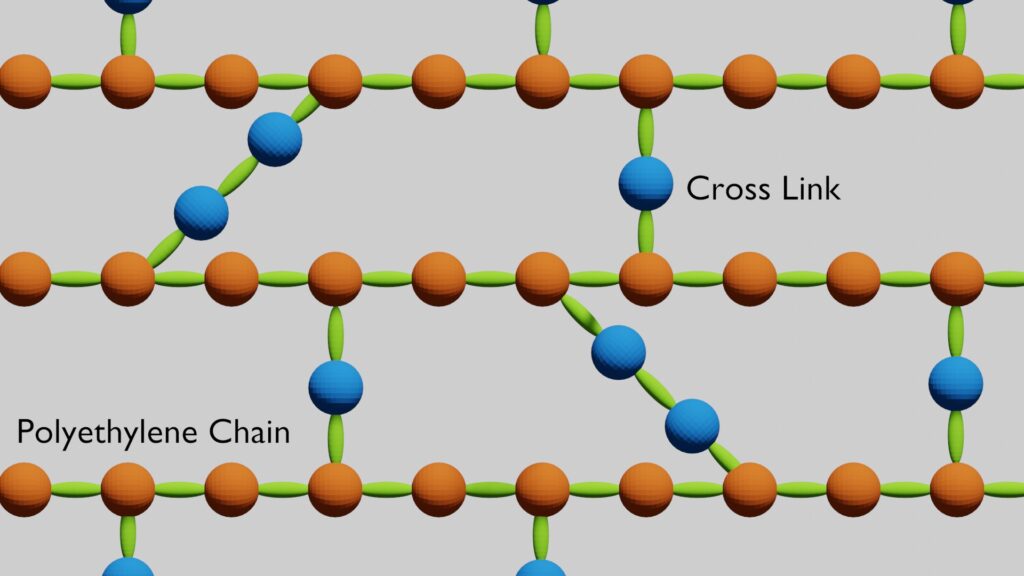
High Thermal Resistance: XLPE can withstand high temperatures. It behaves normal consistently up to 90°C continuous operation and it can withstand up to 250°C during short-circuit. XLPE does not get soften or melt on these temperature, unlike standard polyethylene (PE) or high density polyethylene (HDPE).
Superior Electrical Insulation: XLPE has higher dielectric strength than standard polyethylene and high density polyethylene.
Chemical and Moisture Resistance: An XLPE insulation does not get much affected by soil chemicals, acids, and alkalis hence it has prolong longevity. Unlike oil-paper insulation, XLPE does not absorb moisture, reducing the risk of insulation breakdown.
Mechanical Durability: XLPE possesses very high tensile strength. It has good impact resistance. It is very mechanically flexible.
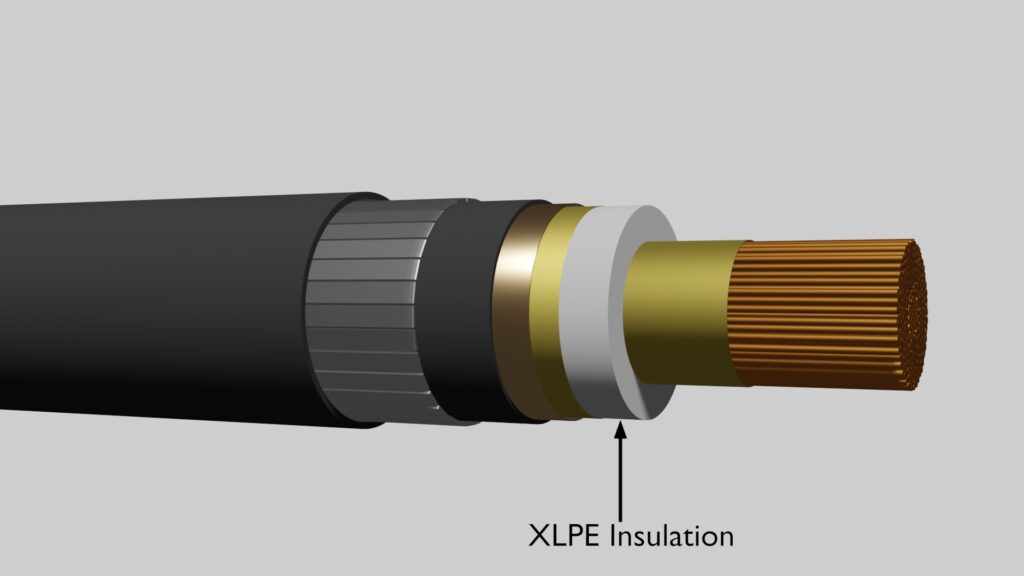
Types of XLPE
XLPE is produced through a process called cross linking, which can be done in three different ways. Based on the production process XLPE categorized as
- Peroxide Cross Linking (PEX A): Most common in HV cables.
- Silane Cross Linking (PEX B): Used for plumbing and lower voltage applications.
- Radiation Cross Linking (PEX-c): Used for specialized applications.
Peroxide Cross-Linking (PEX-A)
Peroxide cross-linking, also known as PEX-A, is one of the most effective methods used to create cross-linked polyethylene (XLPE). This process is widely used in high-voltage power cables because it enhances the thermal, mechanical, and electrical properties of polyethylene.
- The process starts with high-density polyethylene (HDPE), which has long molecular chains but lacks cross-linking.
- HDPE is a good insulator but softens at high temperatures, making it unsuitable for high-voltage applications.
- A special chemical called organic peroxide (such as dicumyl peroxide or benzoyl peroxide) is mixed with polyethylene.
- The peroxide acts as a cross-linking agent, meaning it helps bond polymer chains together.
- The mixture is heated to around 200-250°C. At this temperature, the peroxide decomposes into free radicals, which attack the polyethylene chains and create chemical bonds between them. This forms a three dimensional polymer network, which is what makes XLPE different from regular high density polyethylene (HDPE).
- Once cross-linking is complete, the material is cooled and solidified, locking the polymer structure in place. This final product is PEX-A or XLPE. Now, it has much better thermal resistance, electrical insulation, and mechanical strength than normal or high density polyethylene.