Conductor of an EHV Cable
This is the main part of the cable. The one and only purpose of a cable is to carry electric current. The conductor performs that task. The conductor of an EHV XLPE cable is normally stranded. It is needless to say that the stranding is done to reduce the skin effect and increase the alternating current ampacity of the cable. Normally, hard-drawn aluminum or annealed copper is used for this purpose. Here, it is to be noted that when we use copper as the conductor of a cable, we use annealed copper and not hard-drawn copper. On the other hand, when we use aluminum as the conductor of a cable, we use hard-drawn aluminum but not annealed aluminum.
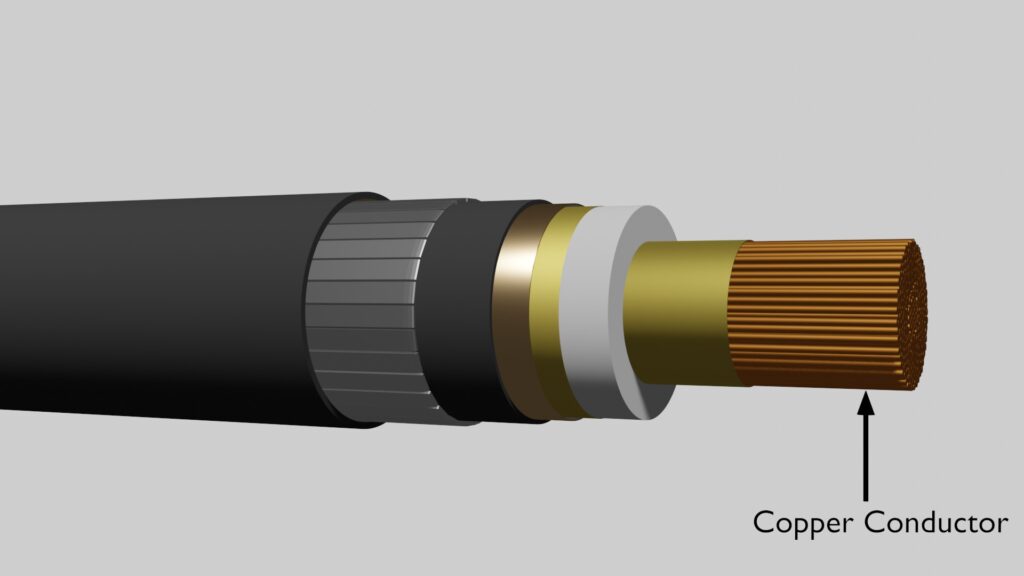
Hard-drawn Aluminum or Annealed Copper
Although the ampacity of annealed aluminum is higher than that of hard-drawn aluminum, we still use hard-drawn aluminum as a cable conductor because it is much stronger. Aluminum is a soft metal, and annealing makes it even softer. Annealed aluminum is too soft and less durable, making it unsuitable for this purpose. Hard-drawn aluminum can handle mechanical stresses like tension and pulling, which is important for demanding applications like EHV XLPE cables.
For copper, we use annealed copper instead of hard-drawn copper. Annealed copper is flexible and easy to work with, making it ideal for bending and installing cables without breaking. Copper is already a much stronger metal than aluminum, so it doesn’t need extra processing like hard-drawing; rather, it is made softer through the annealing process. Hard-drawn copper, while stronger, is too stiff for most cable designs and doesn’t provide any real benefit. That’s why each type is chosen based on what works best.
Conductor Screen of an EHV Cable
The Conductor Screen is a vital part of an Extra High Voltage (EHV) cable. The only purpose of the conductor is to carry electric current but in an EHV cable above 66 kV voltage rating needs help to handle the intense electric field. That’s where the conductor screen comes in. The conductor screen is a thin layer wrapped around the conductor. Normally, it is made of a semi-conductive material, like a polymer or polyethylene mixed with carbon. In an EHV cable, the extra high voltage creates a strong electric field around the conductor. If you leave the conductor bare, that field gets uneven—especially with a stranded conductor, where there are tiny gaps and edges. This unevenness can cause stress points, leading to partial discharges. Those discharges can damage the XLPE insulation over time. The conductor screen fixes this. It smooths out the electric field, making it uniform.
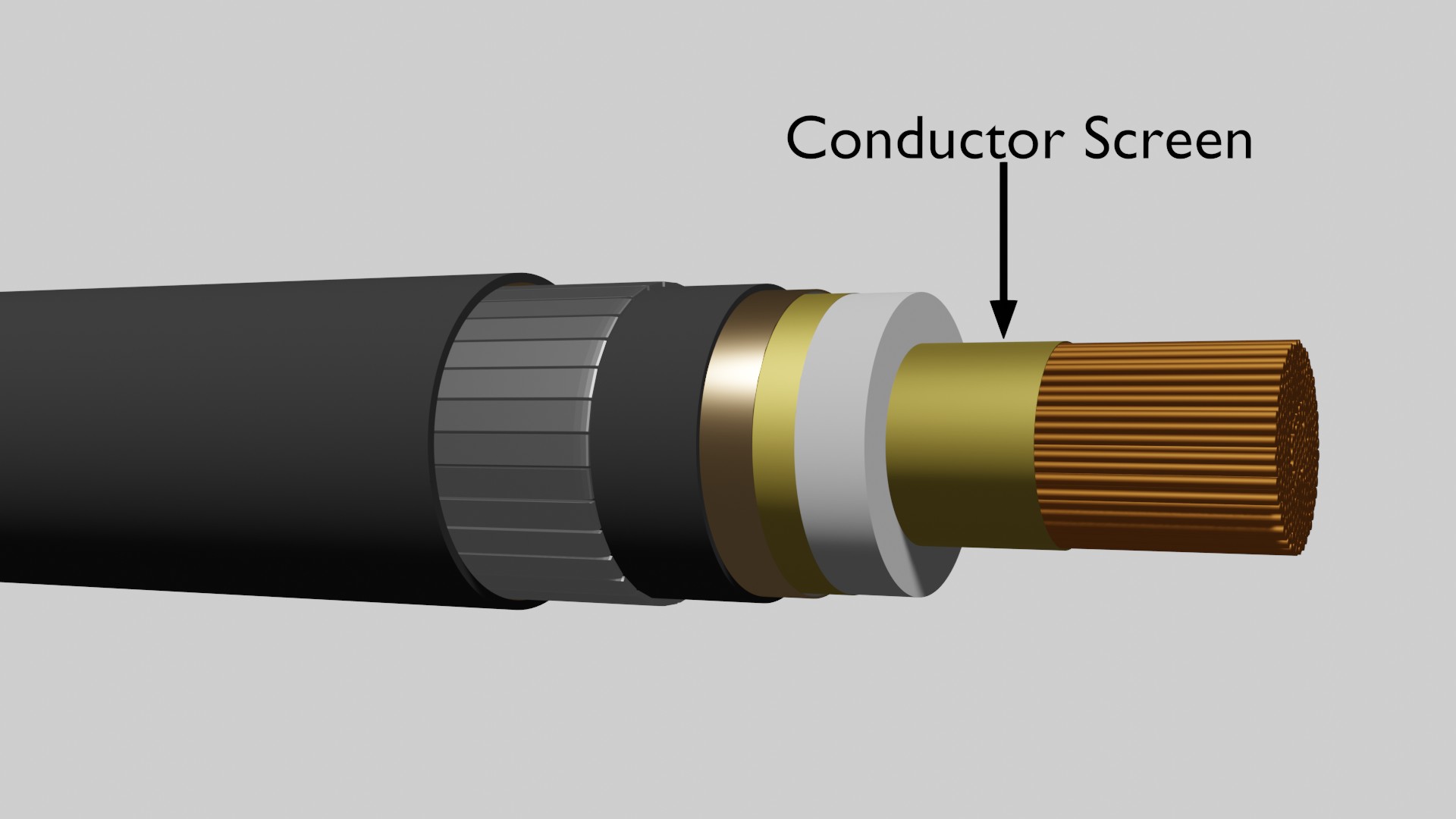
The conductor screen is semi-conductive, not fully conductive like the conductor itself. This means it conducts just enough to spread the electric field evenly across its surface. By doing this, it prevents the field from spiking at any one spot. The conductor screen is usually extruded over the conductor at the same time as the insulation. This ensures a tight bond with no air gaps. In standards like IS 7098 (Part 3) for EHV XLPE cables in India, or IEC 60840, this layer has to meet strict rules. It’s tested for smoothness, thickness (usually a few millimeters) and conductivity to make sure it does its job right.
XLPE Insulation of an EHV Cable
XLPE, or cross-linked polyethylene, is a tough plastic made by linking polyethylene molecules using heat or chemicals. It is extruded over the conductor screen and acts as insulation with its high dielectric strength. It performs steadily up to 90°C and can handle up to 250°C in emergencies. Plus, it resists water, making it ideal for buried and submarine cables.
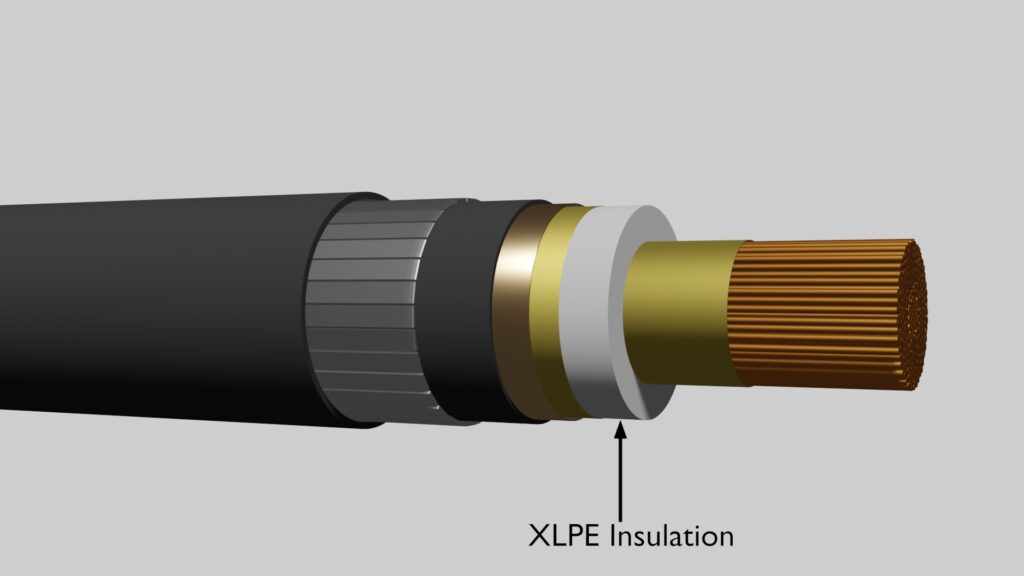
XLPE insulation is extruded over the conductor screen in an ultra-clean process because even a tiny dust particle can trigger discharges that ruin it. Standards like IS 7098 (Part 3) and IEC 60840 demand a smooth, flawless finish, and it goes through tough high-voltage and partial discharge tests to make sure it won’t fail.
Insulation Screen of an EHV Cable
The insulation screen is a thin, semi-conductive layer made from a polymer like polyethylene mixed with carbon black. Its main purpose is to control the electric field outside the insulation. Without it, the field can become uneven, creating stress points that lead to partial discharges. In extra-high voltage (EHV) cables, where the voltage is extremely high, the electric field doesn’t just stop at the insulation rather it may extend outward. If there’s no insulation screen, the field becomes uneven, especially at the boundary between the insulation and the next layer. This unevenness causes stress points that can weaken the insulation over time. Since the screen is semi-conductive, it helps to spread the field evenly.
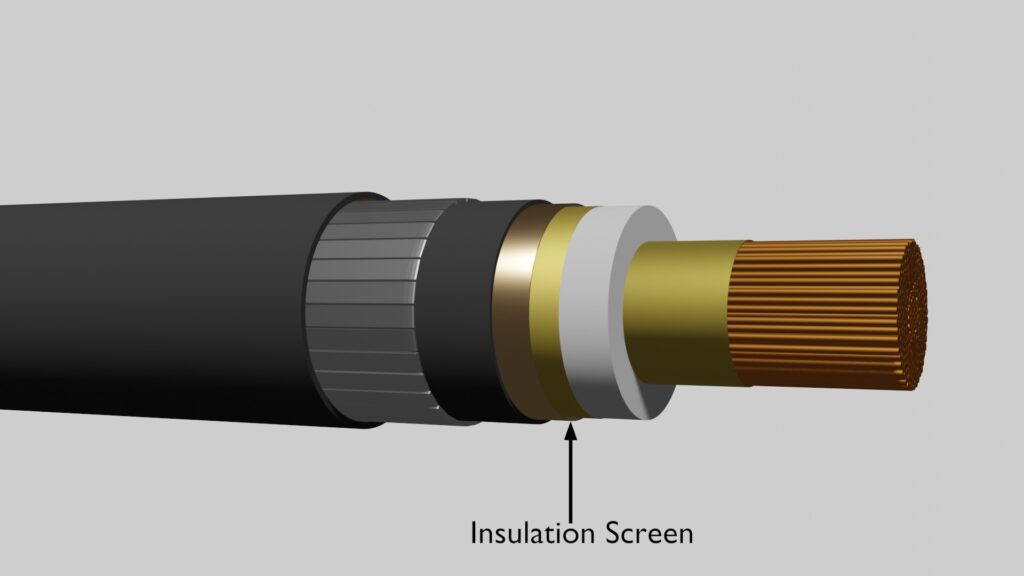
The insulation screen is applied directly over the XLPE insulation during the extrusion process, along with the conductor screen. It plays a key role in protecting the insulation by reducing electrical stress at its surface. It also acts as a barrier between the XLPE insulation and the metal sheath, preventing direct contact and lowering the chances of electrical and mechanical damage. Standards like IS 7098 (Part 3) in India and IEC 60840 ensure that the screen is smooth, a few millimeters thick, and capable of passing tests for partial discharges and voltage endurance.
Metallic Sheath of an EHV Cable
The metallic sheath is a solid metal layer placed around the insulation screen. It’s usually made of lead, aluminum, copper tape, or sometimes corrugated stainless steel. In EHV cables, it sits over the insulation screen, acting as a shield for everything inside. The main purpose of the metallic sheath is to protect the inner conductor from any external magnetic field and also minimize the influence of its own magnetic field to the outer telecommunication line. EHV cables face tough conditions—wet soil, salty water, and rocky trenches. Water is the biggest problem. If it gets inside, it slowly damages the XLPE insulation. The metallic sheath blocks water from entering, keeping the insulation safe. It also helps in case of faults. It carries fault currents to the ground as it is grounded at either or both ends.
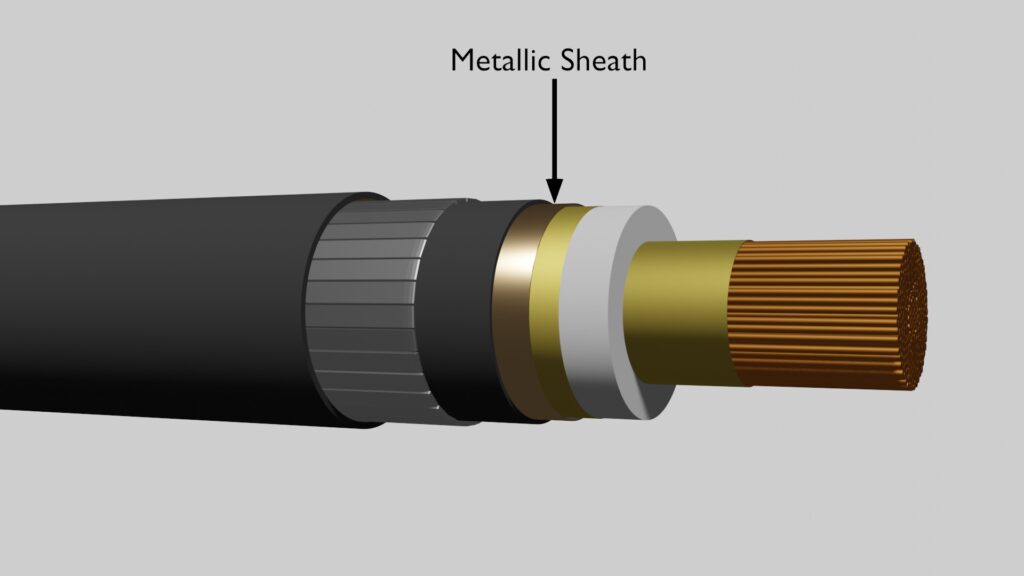
Different metals have different benefits. Lead is heavy but soft, making it easy to bend and seal. Aluminum is much lighter, so it’s better for long-distance cables. Corrugated steel adds extra strength, making the cable more resistant to mechanical damage.
Inner Sheath of an EHV Cable
The inner sheath is a layer, usually plastic like polyethylene or PVC, placed after the metallic sheath. It keeps things tidy and safe inside. EHV cables have to pass through wet ground, rocks, or rough handling during laying. The inner sheath takes some of that pressure off. It smooths out the surface after the metallic sheath goes on clean and tight. It also adds a bit of padding, protecting the metal sheath from getting pinched or cut by armor layers. It’s needless to say this helps the cable stay strong and watertight.
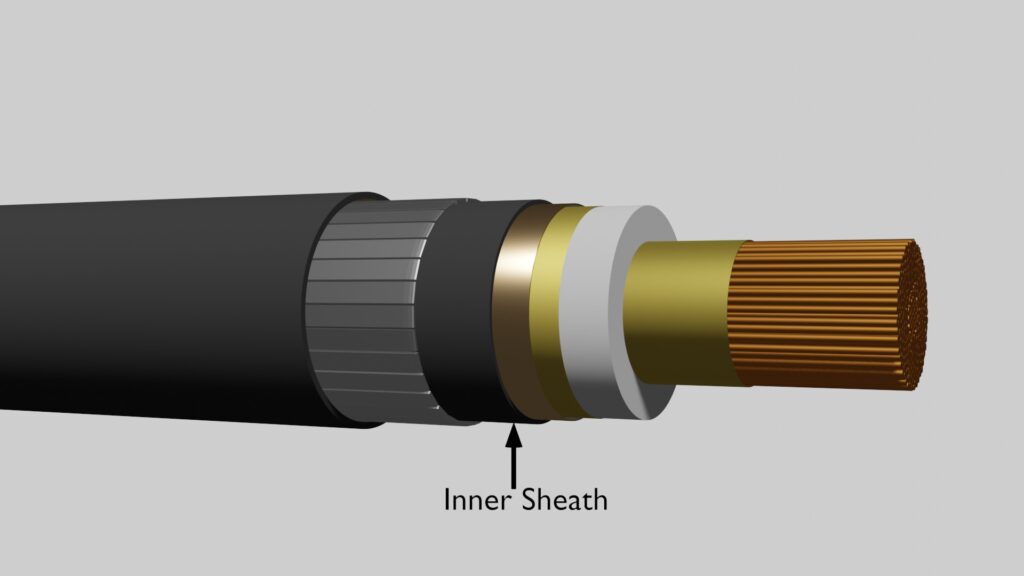
In 3-, 3.5-, or 4-core EHV cables, the inner sheath binds all the cores tightly together.
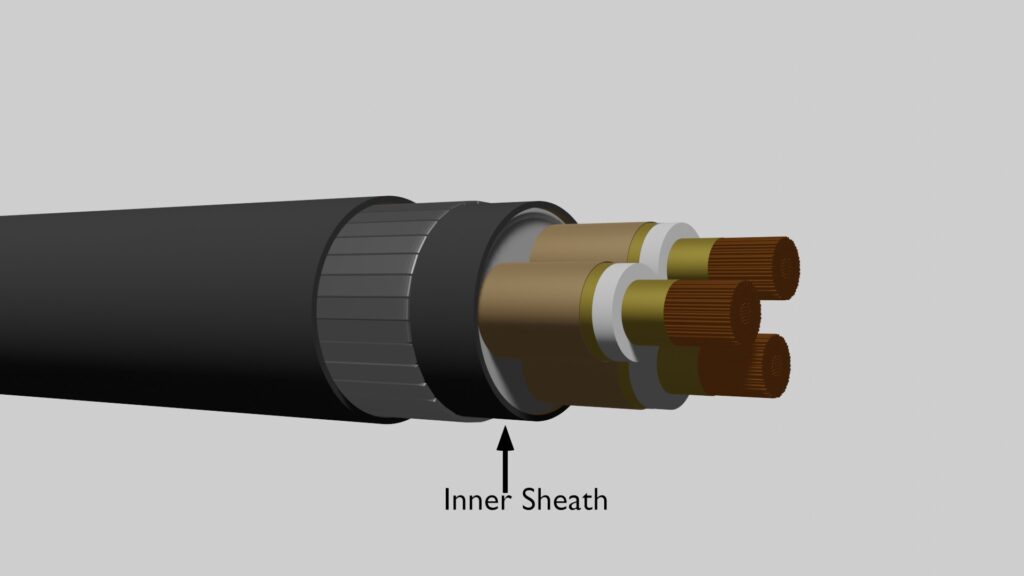
Some power utilities prefer fire redundant inner sheath also.
Armor of an EHV Cable
The armor is a tough metallic layer over inner sheath in an Extra High Voltage (EHV) cable. In an EHV cable, rated 66 kV and up the conductor, XLPE insulation, screens, and metallic sheath need a shield from rough stuff like rocks or digging tools etc. That’s where the armor comes in. It’s usually round steel wires or flat steel strips, wrapped over the inner sheath, under the outer jacket. Armor wire or strips are galvanized steel.
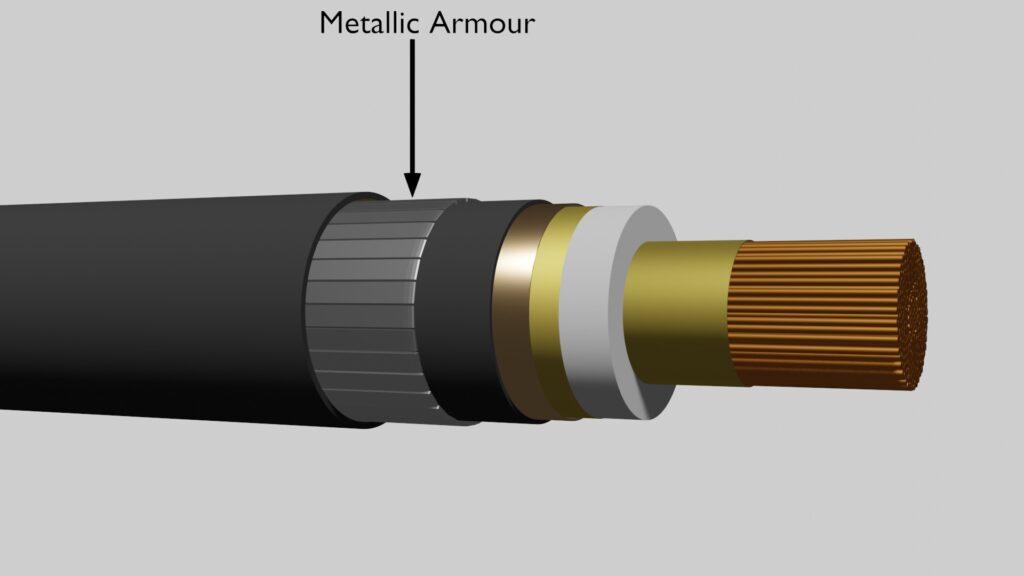
Round steel wire armors are flexible, can easily be twisted in a spiral, easy to bend for tricky installs. Flat strip armor is tough, made of long steel strips at least 0.8 mm thick as per IS 3975. It’s built to handle heavy crushing, especially in deep trenches. Steel is the strongest choice, but aluminum works too if weight or rust is a concern, though it’s weaker.
In some cable designs, armor may not be used. In those cases, the metallic sheath alone serves the purpose of armor. Similarly, in some lower voltage cables, the metallic sheath is not provided; instead, only an armor layer is used, which serves both as magnetic shielding and mechanical protection.
Outer Sheath of an EHV Cable
The outer sheath, also called the outer jacket, is the final protective layer of an EHV cable, shielding it from environmental damage. It’s made from durable materials like polyethylene (PE) or polyvinyl chloride (PVC), with PE being more common for EHV cables. It ensures the cable lasts long by protecting against water, UV rays, and physical damages.
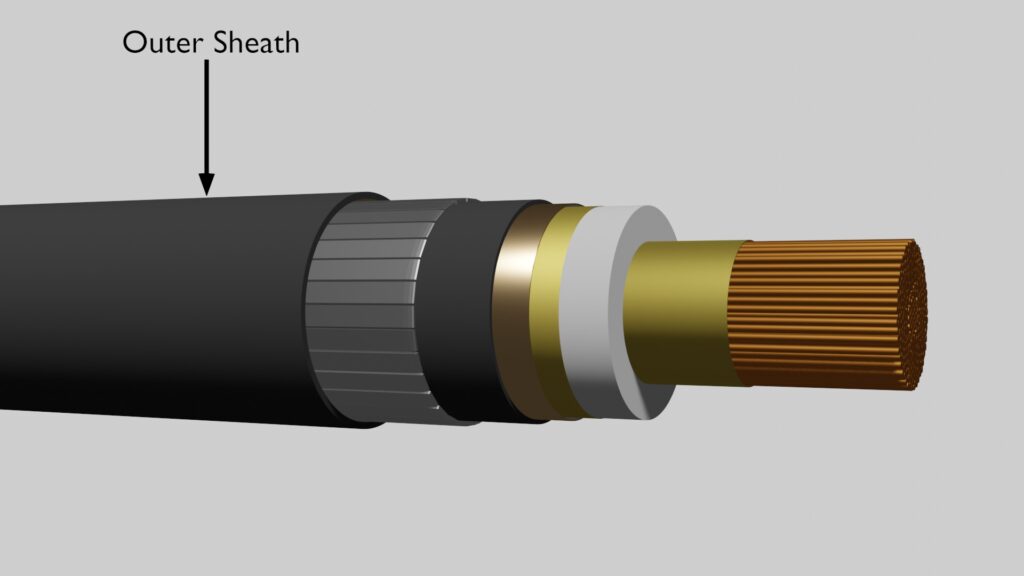
PE, particularly high-density polyethylene (HDPE), is preferred for EHV cables due to its excellent water resistance, flexibility, and high melting point, making it suitable for long-term outdoor and underground installations. It is also UV-resistant when stabilized, which is crucial for cables exposed to sunlight. PVC, on the other hand, is used in some applications for its fire-resistant properties and is often specified in environments where flame retardancy is a concern, such as tunnels or indoor settings. However, for EHV cables, PE is more common due to its superior mechanical and environmental properties. In some cases, low-smoke zero-halogen (LSZH) compounds may be used to meet specific fire safety requirements, particularly in urban or confined spaces, though this is less typical for EHV applications focused on power transmission.
Material | Description | Advantages | Disadvantages |
---|---|---|---|
Polyethylene (PE) | High-density, UV-stabilized polymer | Water-resistant, flexible, durable | May require UV stabilization for sun |
Polyvinyl Chloride (PVC) | Fire-resistant polymer, often used indoors | Flame retardant, cost-effective | Less water-resistant, heavier |
Low-Smoke Zero-Halogen (LSZH) | Fire-safe, low smoke emission polymer | Safe in confined spaces, low toxicity | Higher cost, less common for EHV |