The electricity demand increasing tremendously from last few decades. The increasing demand of lands and few government policies are the constraints in expanding transmission infrastructure. Hence there is no way other than increasing the ampacity of the existing transmission networks. This increases the need for High-Temperature Low-Sag (HTLS) conductors. Among the various HTLS conductors, INVAR core conductor is a robust variant. Invar Core HTLS conductor significantly reduces thermal expansion and mechanical sag, even at higher operating temperatures.
Requirement of HTLS Technology
The melting point of aluminum is 660.3o C. Therefore aluminum can withstand much higher temperature than the maximum operating temperature limit of conventional ACSR conductor. However, at high temperature, the expansion of aluminum is higher than that of steel. Due to this unequal expansion, aluminum strands get looser. The tension of strung conductor totally transfers on the steel reinforce strands. Due to creeping the conductor gets elongated permanently during its operational life. Maintaining ground clearance is critical for an overhead transmission line. Hence, to maintain ground clearance, the ampacity of a transmission line is kept limited. Hence, to increase the ampacity we need to replace the conventional ACSR conductors by any High-Temperature Low-Sag (HTLS) conductor.
What is INVAR?
INVAR is a special nickel-iron alloy, typically composed of 64% iron and 36% nickel. It has extremely low coefficient of thermal expansion. It is as low as 1.2 × 10⁻⁶ /°C, compared to 13 × 10⁻⁶ /°C for steel. This makes INVAR highly resistant to expansion under heat.
Why Use INVAR in HTLS Conductors?
In conventional ACSR (Aluminum Conductor Steel Reinforced) conductors, sag increases significantly over time due to the differential thermal expansion of steel and aluminum strands. INVAR core conductors mitigate this issue by offering a substantially lower thermal expansion coefficient. The INVAR core maintains dimensional stability even at elevated temperatures up to 210°C. While the mechanical strength of INVAR is somewhat lower than that of steel, its superior thermal stability and adequate tensile capacity make it a suitable choice for HTLS applications.
Structure of INVAR Core HTLS Conductors
The typical construction of an INVAR core HTLS conductor includes its reinforce core and outer conducting layer. Pure INVAR or Aluminum-clad INVAR is used for the central core. Aluminum cladding is applied over the INVER strands of the core to prevent corrosion, to improve compatibility with outer aluminum layers, and to minimize galvanic action.
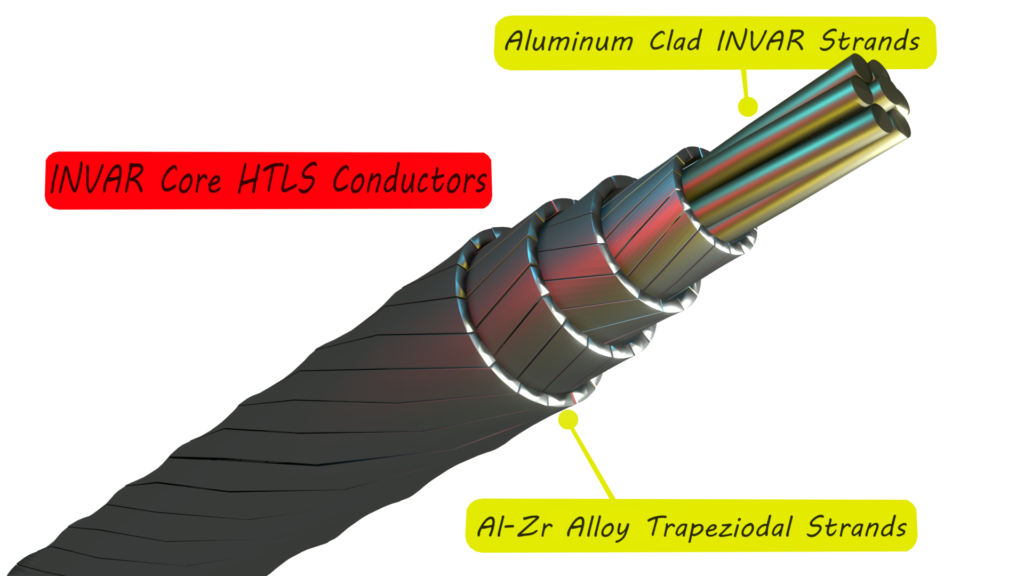
The strands of the outer conducting layer are made of a thermal-resistant aluminum alloy. An aluminum-zirconium alloy, such as Al-Zr AT3, is commonly used for this purpose. The conductor strands are typically annealed or soft-drawn to enhance their thermal performance. Trapezoidal strand geometry is often employed to minimize inter-strand gaps. This increases the packing density of the aluminum alloy. As a result, the available current-carrying cross-sectional area is enhanced.
Challenges and Considerations of INVAR Core HTLS Conductors
The long-term thermal cycling may cause fatigue if not designed properly. INVAR and aluminum cladding increase material cost. INVAR is less ductile than steel. Therefore, INVAR Core HTLS Conductors must be handled carefully during installation.